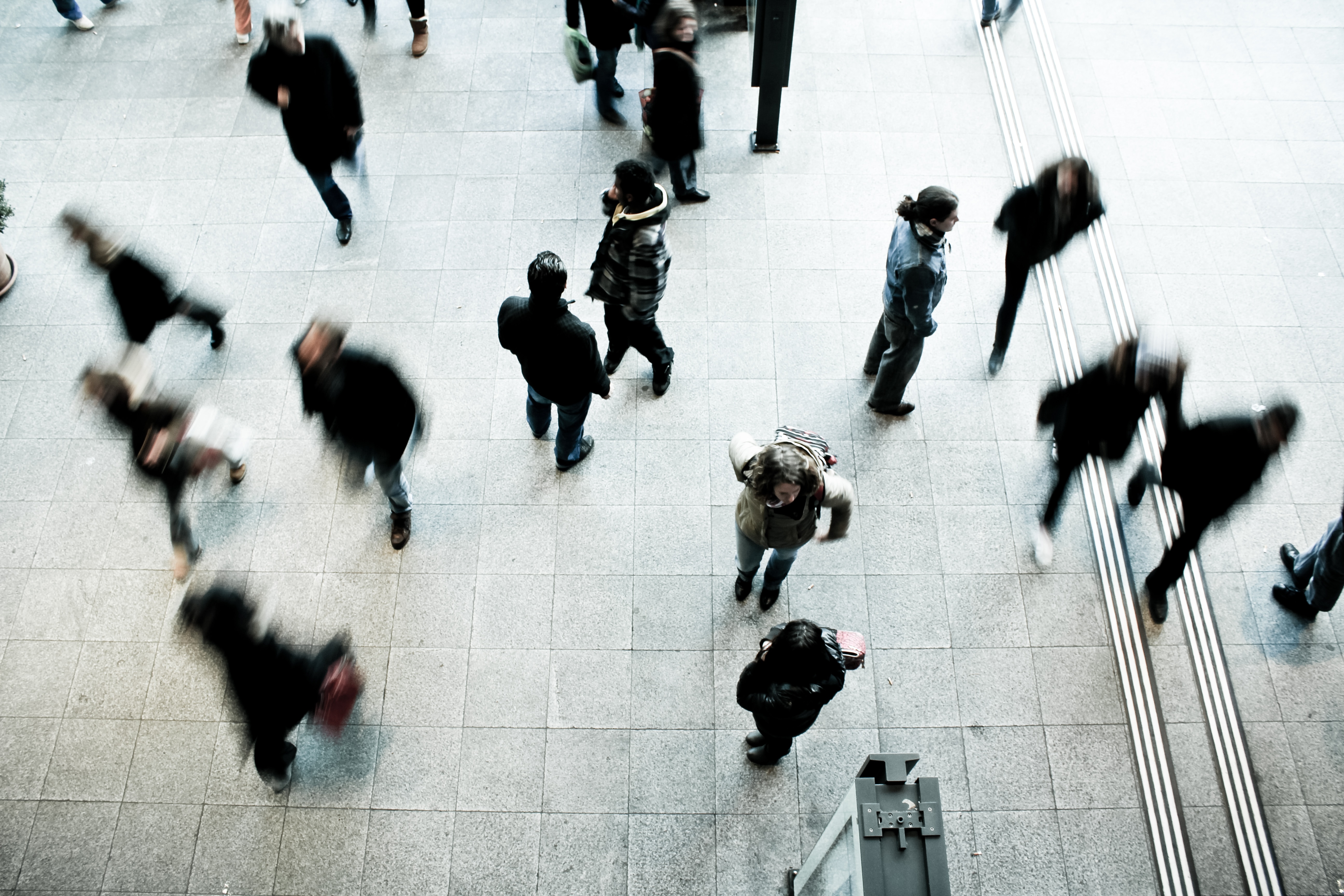
GE Aviation transforms Buncombe County’s workforce and community
Asheville -- Asheville Chamber of Commerce News September 17, 2019
In the state of North Carolina, GE Aviation employs more than 1,800 residents. GE also compensates those employees more than 2x the state average, and has been estimated to create a total economic impact of $7.2 billion per year for the Tar Heel state. While these numbers are astounding, they tell only half the story of GE Aviation’s effect on its surrounding communities, especially here in Buncombe County.
“The vision and story for our site here is transformation,” says Tyler Reed, rotating parts plant leader at GE Asheville. “We are always working to improve our people and operation by embracing a problem solving and continuous improvement culture. It is exciting to think about transformation as this site has been around for 70 years and has built a great legacy. We are seeing a 40% increase in demand hours over the next five years and we must continue to evolve or “transform” to meet this demand. The aviation manufacturing environment has shifted and so has our strategy to spur and sustain growth. I’m thrilled to lead this team as we adapt to win during our most defining time of innovation.”
It all starts with the people. GE Aviation invests hundreds of millions a year on training and professional development for its 50,000 employees around the world. There are more than 700 GE Aviation employees in Buncombe County, and that number continues to grow. Through a robust apprenticeship program, GE trains high school students at such a sophisticated level that, upon graduation, students are qualified to sign on as full-time employees. This local program is considered the gold standard of apprenticeship programs nationwide. To further encourage this talent pipeline, in 2017 the GE Foundation presented Pisgah High School with a $100,000 grant to be used for its machining and metals department, guaranteeing a brighter future for the students and families within our community.
This practice of growing talent happens at every step along the way. In 2013, GE Aviation Asheville formed a successful partnership with AB Tech to create a training center that provides courses for prospective employees who want to work but lack the necessary technical skills. For undergraduates, GE offers leadership development programs for future engineers, supply chain leaders and human resource specialists. There’s also training programs available for current employees who are interested in progressing and building new skills.
“In almost every function inside of this building, we have a fluid plan for you to learn more and work your way up. At the core of every position is growth and opportunity. GE builds from the assets it has – its people. We want you — and help you — get further, faster,” explains Steven Johnson, rotating parts HR leader. “And the amount of previous education an employee has isn’t a barrier. If you have work experience and you have the capabilities that we look for, we really try to utilize that.”
As for Reed’s vision of transformation, his description of GE Aviation Asheville’s changing approach to its manufacturing process sums it up best. At the rotating parts facility, leadership is shifting gears from “job shop” to “volume production shop.” In layman’s terms, Reed explains, rather than making one hundred parts perfect, his team’s new mission is creating agile processes to produce one perfect part one hundred times. To accomplish that goal, they’re leveraging technical insights from their highly skilled workforce and investing in technology to destroy the limitations of today and disrupt the manufacturing landscape of tomorrow.
This shift has allowed Reed’s site to diversify its portfolio to pursue more military work, strategically positioning themselves at the forefront of blossoming helicopter engine programs and continue competing for global projects. “Our competitiveness has allowed us to pull work from Asia, Eastern Europe, China and Turkey to expand our manufacturing footprint in the U.S. It’s what will continue to win business that will support American job growth for years to come”, adds Steven Johnson.
While Asheville’s rotating parts manufacturing model grows increasingly sophisticated and profitable, it continues to look for ways to transform the surrounding community. In 2017, GE’s statewide charitable contributions totaled more than $2 million. In 2018, GE Aviation employee Katie Schafer was one of four Asheville women to receive a WomanUP’s Rising Star Award for her exceptional commitment to breaking down barriers for women in aviation. And in 2019, GE Aviation Asheville won United Way’s “Hands On Business Partner of the Year” award for the success of its STEM Kit program.
This project engaged 200 4th and 7th grade students in Asheville City and Buncombe County Schools. To amplify its power and potential, GE Aviation developed the STEM kits based on grade-level insights from local education specialists, like Stefanie Buckner, K-12 Math Specialist for Buncombe County Schools. “I don’t think our students realize what we have here or what opportunities exist for them to be able to stay and thrive in this area. It’s really helpful for parents to understand that major manufacturing is happening — right in their backyards — at GE Aviation in Asheville — and there are great job opportunities within this field,” Buckner adds.
As Tyler Reed and his team consistently push toward the future, their local reach isn’t lost. It’s part of the ride. “I love seeing how dramatically this site lifts up our community. From jobs to stability and real cultural impact, we’re both a force for good and a force for growth. It’s been incredible to see GE Aviation Asheville take flight,” says Reed.